Our Services
What we do
PLC Programming and Design
Our company boasts professionals and operators in its staff with the necessary skills to be able to offer our customers solutions that are extremely tailored to their needs. Going into more detail, we also and above all deal with PLC programming and design. The beating heart of our work is PLC software design.
The PLC programmer develops, designs and tests application software for industrial machinery and automated systems, whose operation is regulated by programmable logic controllers (Programmable Logic Controller, or PLC). The PLC is an industrial computer that controls the operation of the machine based on the program set by the user.
It is a programmable logic device characterized by great robustness and reliability, very widespread in the industrial automation sector: in fact, it can remain in operation 24 hours a day, even in critical conditions of temperature, humidity, vibrations or electromagnetic disturbances. Through input devices, called inputs, the PLC receives digital and analog signals that it processes thanks to the microprocessor (CPU) to operate certain output devices, according to the instructions of the stored program. For example, the PLC interacts with the control circuit to turn the machine on/off when a certain temperature is reached, open/close valves based on predefined pressure parameters, etc.
The PLC programmer studies the requirements of the program to be created and defines the technical specifications of the project, designs the interaction diagrams between electrical and electromechanical components, inputs and outputs, structures the program sequences according to the assigned specifications and designs the logical flow diagrams. He then takes care of writing the program, using specific PLC programming devices.
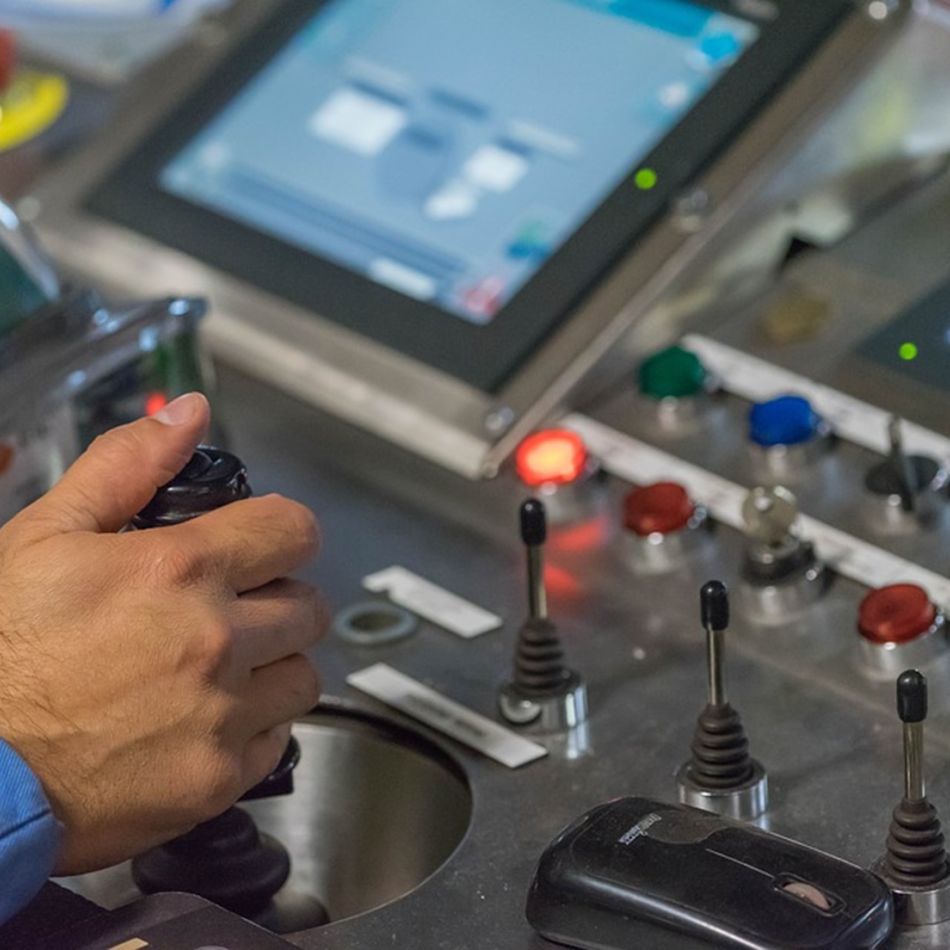
Testing
Once the development of the automation software is completed, the testing phase begins, in which any malfunctions are resolved. Testing is probably the longest part of the job and includes a wide variety of tasks:
- Checking all the electrical parts of the machine (e.g. Power supplies, direct motors, safety transformers, etc.)
- Installing and programming all the software present (HMI, safety electronics, cameras, etc.)
- Loading the PLC software program onto the machine through the interface and checking the start-up of the machine or automated system.
- Performing I/O (input/output) tests and tests to ensure that the program works as expected and does not have errors (bugs), establishing the criteria and procedures for technical checks and checking that certain quality standards are achieved.
- Checking all safety devices
Design of HMI SCADA Systems
Our company deals, among other services, with the design and construction of HMI – SCADA systems.
It can also handle the configuration of control interfaces, such as HMI (Human Machine Interface), MMI (Man Machine Interface), OIS (Operator Interface System), OIP (Operator Interface Panel) or SCADA (Supervisory Control And Data Acquisition) interfaces.
This is a type of system that has been on the market for thirty years and has evolved thanks to processes and technological innovations. In particular, we provide, to best manage the production processes of your company, a specific system that, using sensors and actuators, will be able to reliably supervise all phases of the production process.
We use quality, reliable and functional devices as they are made by prestigious manufacturers and brands. We will implement a specific system that will be composed of sensors that will collect important data in the field that will be sent to the supervisor through a specific control system who, based on the findings, will have to evaluate whether everything is proceeding in the best possible way and, if necessary, make changes to the process by sending specific information to the actuators.
Automatic Machine Wiring
The automatic machine wirer is responsible for the correct connection and installation of electrical components within an automated equipment or system. This work can be divided into several phases:
-
Drawing Analysis: Initially, the wirer must examine the drawings and electrical diagrams provided by the designer. This step is crucial to understanding the layout and connection of the components.
-
Material Preparation: Acquires and organizes all the materials needed for the wiring, ensuring that they comply with the project specifications.
-
Actual Wiring: Physically connect the electrical components according to the provided diagrams. This process requires attention to detail and precision to ensure accurate wiring.
-
Test and Verify: After wiring, the wireman performs tests to ensure all connections are correct and the system is working as expected. Corrections are made if necessary.
-
Documentation: Detailed records of all connections made and any changes made during the process. This documentation is essential for future maintenance and troubleshooting.
Electrical Diagram Design
The electrical designer is responsible for developing and planning electrical systems for various applications. This professional analyzes project needs, draws up electrical schematics, selects appropriate components, and specifies details such as wiring and protective devices. Collaborates with other team members, such as electrical engineers and technicians, to ensure project consistency and standards compliance. The work of the electrical designer also includes drafting technical documentation and supervising the practical implementation of his projects.